An Unbiased View of Alcast Company
An Unbiased View of Alcast Company
Blog Article
Alcast Company Things To Know Before You Buy
Table of ContentsThe Buzz on Alcast Company10 Easy Facts About Alcast Company ShownAll about Alcast CompanyThe 25-Second Trick For Alcast CompanyAlcast Company Can Be Fun For AnyoneGetting The Alcast Company To Work
The subtle distinction depends on the chemical content. Chemical Contrast of Cast Light weight aluminum Alloys Silicon promotes castability by reducing the alloy's melting temperature level and enhancing fluidness during spreading. It plays an important duty in allowing detailed molds to be filled properly. Additionally, silicon adds to the alloy's stamina and put on resistance, making it valuable in applications where longevity is essential, such as vehicle parts and engine parts.It likewise improves the machinability of the alloy, making it simpler to process into completed products. This way, iron adds to the total workability of light weight aluminum alloys. Copper boosts electric conductivity, making it useful in electric applications. It likewise improves rust resistance and adds to the alloy's total toughness.
Manganese contributes to the strength of light weight aluminum alloys and enhances workability. Magnesium is a light-weight element that gives stamina and influence resistance to aluminum alloys.
How Alcast Company can Save You Time, Stress, and Money.
Zinc boosts the castability of light weight aluminum alloys and aids control the solidification process during casting. It boosts the alloy's strength and hardness.
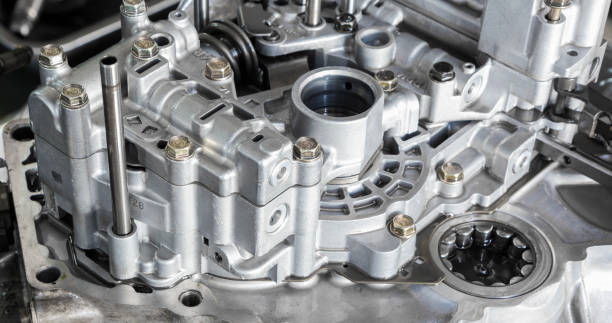
The main thermal conductivity, tensile stamina, yield stamina, and prolongation differ. Amongst the above alloys, A356 has the highest possible thermal conductivity, and A380 and ADC12 have the most affordable.
The 8-Second Trick For Alcast Company
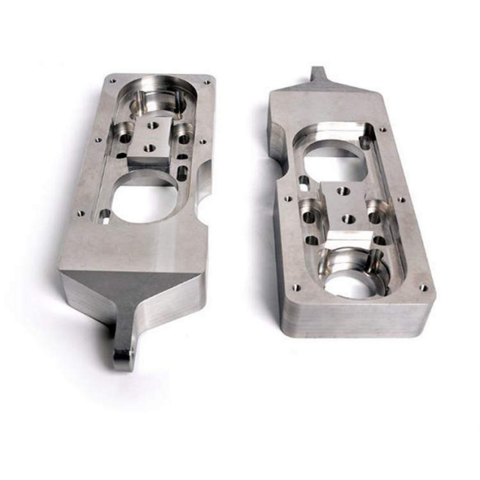
In accuracy casting, 6063 is appropriate for applications where intricate geometries and top notch surface coatings are vital. Instances consist of telecommunication rooms, where the alloy's superior formability enables streamlined and visually pleasing layouts while preserving architectural honesty. Similarly, in the Illumination Solutions sector, precision-cast 6063 elements produce classy and efficient illumination fixtures that call for intricate shapes and excellent thermal performance.
The A360 shows remarkable prolongation, making it excellent for facility and thin-walled elements. In accuracy casting applications, A360 is well-suited for sectors such as Consumer Electronics, Telecommunication, and Power Tools.
The Best Strategy To Use For Alcast Company
Its special residential properties make A360 a valuable selection for precision casting in these industries, boosting product longevity and quality. Aluminum alloy 380, or A380, is a commonly used casting alloy with several distinct qualities. It uses excellent castability, making it an ideal option for accuracy spreading. A380 shows great fluidness when molten, ensuring elaborate and in-depth mold and mildews are accurately recreated.
In accuracy casting, light weight aluminum 413 shines in the Customer Electronic Devices and Power Devices sectors. This alloy's remarkable corrosion resistance makes it an outstanding option for exterior applications, making sure lasting, long lasting items in the stated industries.
The Greatest Guide To Alcast Company
The light weight aluminum alloy you choose will significantly influence both the spreading process and the properties of the last item. Due to the fact that of this, you must make your choice thoroughly and take an enlightened strategy.
Figuring out the most ideal light weight aluminum alloy for your application will suggest considering a large array of qualities. The very first category addresses alloy characteristics that affect the production process.
The Best Strategy To Use For Alcast Company
The alloy you read the full info here select for die casting straight impacts numerous elements of the casting process, like how very easy the alloy is to work with and if it is prone to casting issues. Hot splitting, also called solidification cracking, is a regular die casting defect for light weight aluminum alloys that can result in inner or surface-level splits or splits.
Certain light weight aluminum alloys are much more susceptible to hot fracturing than others, and your choice ought to consider this. An additional common flaw located in the die casting of light weight aluminum is die soldering, which is when the cast adheres to the die walls and makes ejection tough. It can harm both the cast and the die, so you need to search for alloys with high anti-soldering residential properties.
Deterioration resistance, which is currently a noteworthy quality of aluminum, can vary substantially from alloy to alloy and is a necessary particular to consider depending on the environmental conditions your product will be subjected to (aluminum casting company). Put on resistance is another residential property generally looked for in light weight aluminum items and can distinguish some alloys
Report this page